Ce-Preg® - Thermoplastische Prepregs
Musterfertigung
Das Cetex Institut hat ein Verfahren und eine Prototyp-Anlage entwickelt, die die Fertigung vorimprägnierter unidirektional endlosfaserverstärkter thermoplastischer Prepregs – unter der Bezeichnung Ce-Preg® - ermöglicht. Sie bilden das Ausgangsmaterial für den späteren multidirektionalen Schichtaufbau zur Herstellung belastungsgerechter Mehrschicht-Laminate im In-Line-Prozess. Durch Verpressen der plattenförmigen Halbzeuge können diese Mehrschicht-Laminate mit gezielter Faserorientierung zu 3D-konturierten Bauteilen weiterverarbeitet werden.
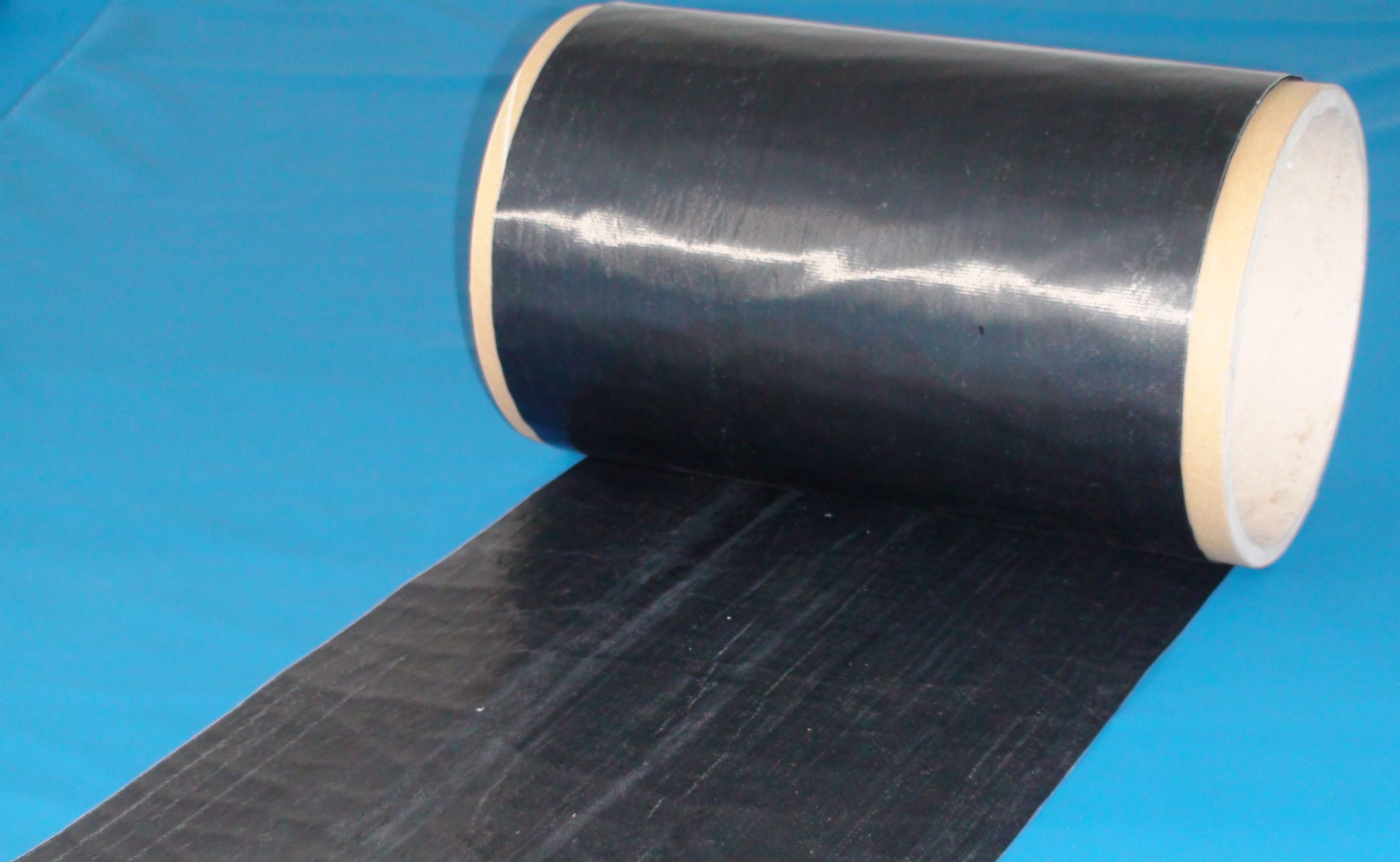
Thermoplastische Prepregs
Die thermoplastischen Prepregs Ce-Preg® bestehen aus einer unidirektional ausgerichteten und ausgebreiteten Verstärkungsfaserschicht (Carbon-, Glas-, Basaltfasern), die in eine Matrix aus thermoplastischem Kunststoff (Polyamid, Polypropylen, ...) eingebettet ist. Die parallele Ausrichtung und gestreckte Lage der Fasern führt zu einer hohen Ausnutzung der spezifischen Festigkeitseigenschaften der Verstärkungsfasern. Die vollständige Einbettung der Fasern in die Matrix schützt vor Faserschädigung bei der Weiterverarbeitung. Entsprechend der Anforderungen an die Faserverbundbauteile können unterschiedliche Faser-Matrix-Kombinationen und verschiedene Faservolumengehalte realisiert werden. Damit wird es möglich, die Werkstoffeigenschaften in einem weiten Bereich variabel einzustellen.
Bei der kontinuierlichen Herstellung des UD-Prepregs werden auf eine unidirektional ausgerichtete Faserschicht mit definierter Flächenmasse von beiden Seiten thermoplastische Folien aufgebracht und die Faservorlage mit der aufgeschmolzenen Thermoplastmatrix imprägniert. Es entsteht ein im konsolidierten Zustand flexibles, unidirektional endlosfaserverstärktes thermoplastisches Prepreg mit einem vorgegebenen Faservolumengehalt.
Weiterverarbeitung
Das aus einem unidirektional endlosfaserverstärkten thermoplastischen Prepreg bestehende Halbzeug kann in dieser Form oder als belastungsgerecht aufgebauter Mehrschichtverbund sowohl durch einen thermischen Umformprozess im Presswerkzeug als auch mittels Falt-Wickel-Technologie weiterverarbeitet werden.
- Musterbreite: bis zu 350 mm
- Musterlänge: bis zu 1000 m
- Faservolumengehalt: 35 ... 60 %
- Verstärkungsfasern:
- Carbonfasern
- Glasfasern
- Basaltfasern
- Aramidfasern
- Matrixmaterialien (in Abhängigkeit von den verwendeten Fasern)
- PP, PA (PA6, PA6.6, PA12, PA11), PBT, PC, TPU und PE
- Automobil- und Fahrzeugbau
- Boots- und Sportgerätebau
- Architektur und Bauwesen
- Industrieanwendungen
Downloads
Ansprechpartner
Dipl.-Ing. Thomas Bauer
Forschungsbereichsleiter Faser-Kunststoff-Anwendungen
+49 371 5277 225
Per Mail kontaktieren